Ed Cahoj, a cattle farmer in Polk County near Halfway, Mo., remembers the day he became aware of soil fertility. He was 7 or 8 years old on his dad’s farm in Kansas. The land had just been plowed, and like any good farmer, his dad picked up a handful of the freshly turned sod and smelled it.
“It smelled good, like it was alive,” Ed remembered. Then he noticed bits of carbon in the soil and asked when there’d been a fire. “I was raised here, and none in my memory,” his dad answered. That was Ed’s first glimpse of biochar from fires set by Native Americans.
A few decades later in southwest Missouri, Ed was still interested in soil fertility and at the 2009 Ozarks New Energy Conference was intrigued with a presentation by Dr. David Laird from Iowa State University, a leading biochar researcher for the USDA. Over the next few years, Ed and other farmers in the National Biomass Producers Association began researching pyrolysis processors that could produce biofuel and/or biochar from Switchgrass and other biomass.
That led to Ed designing and building his own processor. He concentrated on producing biochar, because, as he said, “It doesn’t matter if the gas tank is full if the refrigerator is empty.” As concern about food security has increased, Ed is convinced that amending the notoriously poor soils of the Ozarks to produce more should be a top priority.
He started small, building a 6-foot by 13-inch processor of his own design, machined locally. He feeds Switchgrass, which he grows; wheat straw, which is readily available; or corn stover into the trough, clamps down the lid, attaches the flue and lights a fire through an intake opening. In less than six minutes, the biomass is reduced to black char. When cooled, he bags it and later mixes it 50/50 with poultry litter. Before planting, he digs a trench, shovels in the biochar mixture, blends the mix with the soil, and plants his seeds and seedlings. The results last summer were amazing. And with a half-life of 1,000 years, a little of the biochar goes a long ways.
Lab analysis of the biochar produced from the processor indicates that it is consistent with Class 1 or high Class 2 biochar, according to the recently determined Biochar Standards, which were approved by the International Biochar Initiative (IBI) group made up of proponents of biochar throughout the world. The IBI also is developing a certification program for biochar that Ed plans to pursue.
“As far as I know, this is the only processor of its kind for herbaceous plants,” he said. He’s simplified the processor to make it as user friendly as possible so that anyone with commonsense and access to the materials can build and use a processor. Depending on labor and metal costs, a processor can be built for approximately $800.
The actual process of producing the char takes some understanding of combustion and a respect for working with very hot materials – flue temperatures can reach several hundred degrees Centigrade. The process can be dusty so Ed advises a face mask. The biochar can be combustible, too, much like coal dust, so properly storing it is a must. He’s found that processing the biochar works best when the humidity is 60 to 70 percent.
Ed believes small processors are the way to go and points out that his can be easily moved from farm to farm. His commitment to stewardship has convinced him to share his knowledge freely for the larger goal of improving soil fertility.
“Caring for the land is in my blood like many other people in agriculture,” Ed said. “We have to get our soil balanced in order to produce more.”
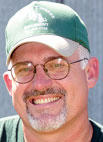